- 设为首页
- 加入收藏
- 无障碍阅读
- 长者版

全厂数智化改造 生产和管理双提效
近日
走进中色大冶冶炼厂智慧运营中心
十多名员工正在电脑前通过
眼前的十几块大屏
实时监控各个车间的画面和数据
从而实现全厂的指挥和调度
通过实时监控屏幕,可以看到车间内鲜有人员活动,但机器却在不停地运转。原来,中色大冶冶炼厂通过DCS控制系统,实现了对整个生产过程的实时监控和自动化管理。在生产流程方面,冶炼厂实现了从熔炼、配料、吹炼到精炼等多个环节的智能化改造。
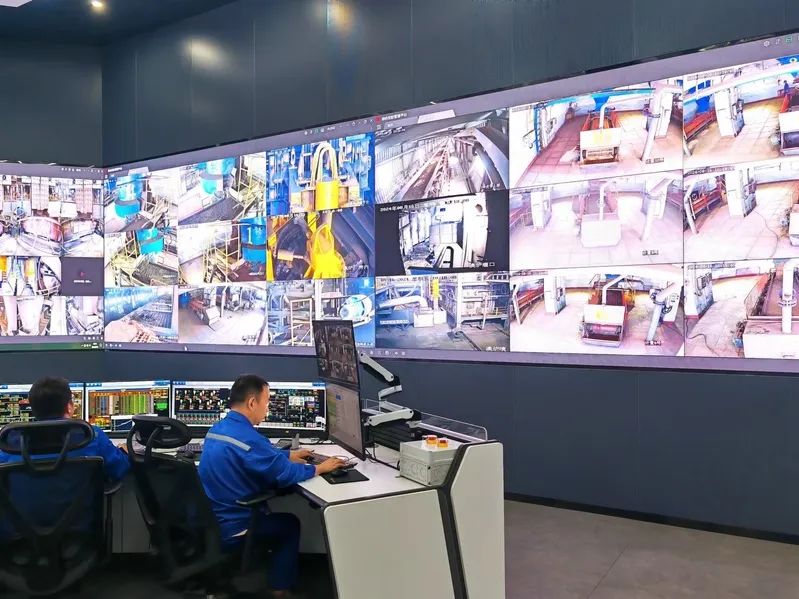
“可以说,这里就是整个冶炼厂的中枢,也是全厂的大脑。通过在智慧运营中心集中办公,实现多工种无边界协同办公,大大提高了生产效率。”中色大冶冶炼厂厂长助理、智慧运营中心主任肖军表示。
据肖军介绍,目前每个班平均13人左右,包括熔炼、配料、吹炼到精炼等各个环节,他们通过大屏监控的画面和数据,及时给车间下达指令,同时上下工序的人还能及时沟通,整个过程既方便又高效。“熔炼、吹炼、制酸全流程操作岗位实现数据互通、集中控制和无边界协同。信息化赋能管理效能提升,推动企业数字化、智能化转型。”肖军说。
“鼠标点了系统里的‘声光报警’按键后,转炉车间会有声光报警提示。然后点击‘转入准备’,系统会判断是否满足一键转入的各项条件。”智慧运营中心一位工作人员介绍,转炉使用红外测温、终点判断,当满足转入条件时,点击“一键转入”按键,车间内的炉体便可以完成倾转,从而实现了远程的“一键摇炉”操作。
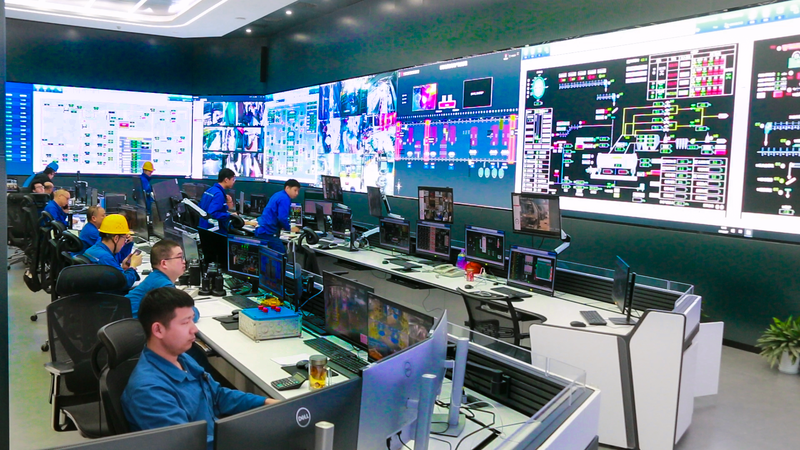
借助“一键摇炉”转炉智能生产系统
中色大冶冶炼厂实现炉体倾转、送风、
供氧、密封小车运行、滑动烟罩开关、
锅炉钟罩阀开关等联动控制
并根据炉子倾转角度的不同
智能化控制开关角度
简化了操作流程,减少了人为失误
而且缩短摇炉时间,减少烟气逸散
得益于该系统
中色大冶在国内首次实现
铜冶炼转炉远程集中控制
“以前我们都在各自的车间做事,而现在我们汇聚在智慧运行中心办公,不仅工作环境焕然一新,而且效率也较以往有了显著提高。”作为冶炼厂拥有24年丰富经验的老员工,澳炉主操杜鹏对工厂的创新变革有着深刻的感触。他表示:“先进的吸尘系统使车间内的环境卫生得到了极大改善,集中办公模式让一些问题可以面对面交流,极大地缩短了问题处理的时间,提升了生产过程的安全性和可靠性,也提高了产品合格率。”
去年,中冶大冶冶炼厂经历了建厂以来停产时间最长的一次升级改造。环保升级及全厂生产系统完善项目总投资7.4亿元,主要改造内容包括备料系统改造、转炉系统改造、环集系统改造、硫酸系统改造、数字化智能化改造等五个方面。而最为重要的是数字化智能化改造,这也是全厂改造最为核心的部分。
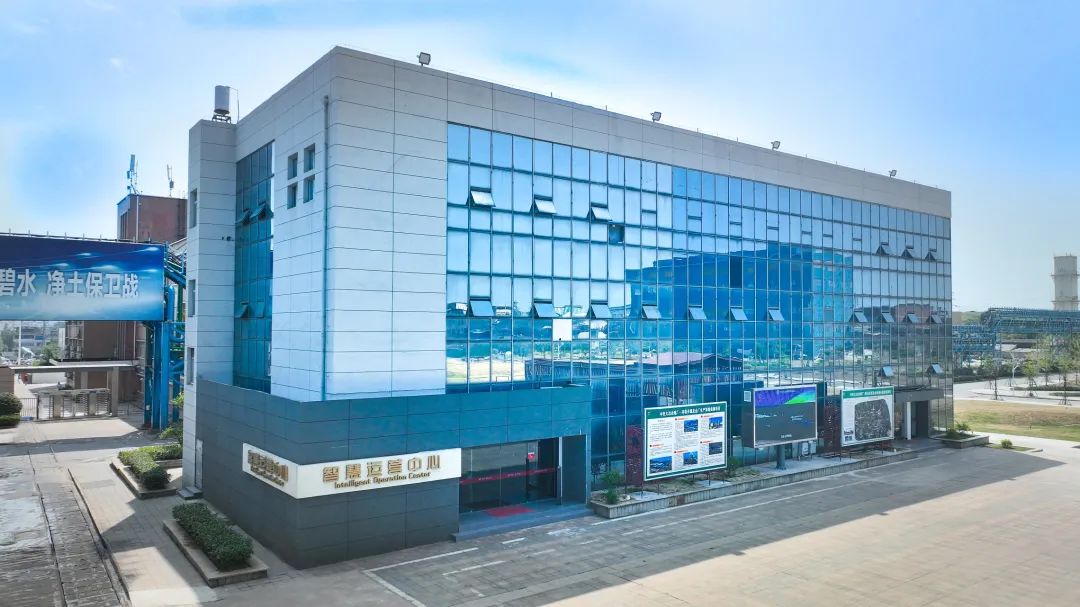
据了解,中色大冶冶炼厂的智能化改造仍在持续推进中。二期项目已经立项,预计在明年逐步完善,将实现更多功能模块的开发和应用。“目前,我们在智能化改造方面处于行业前沿,电解系统、PS转炉和澳炉系统等多项技术和应用处于国内领先水平。”肖军表示,智能化改造的最终目标是实现企业的可持续发展,降本增效的同时,提高了产品质量和生产安全性。
通过装备升级、智能管控、数字赋能
中色大冶冶炼厂作业效率和
劳动生产效率整体提升20%
全厂30余个关键岗位实现了
集中监测、智能测算、自动操控
转炉等艰苦岗位实现了无人化操作
企业经营效益更优
通过流程优化、管理提升
年降本增效超过1.2亿元
企业重生为一座
现代化智能绿色铜冶炼工厂